Focus on Sustainability: How VAUDE Uses Retraced to Improve Supply Chain Transparency
The renowned outdoor outfitter VAUDE has undergone an impressive development since its foundation. The family business was founded in 1974 by Albrecht von Dewitz as a mountain sports outfitter in Obereisenbach near Tettnang in Germany. Since 2009, VAUDE has been under the management of the founder's daughter, Antje von Dewitz, and has developed into a major player in the outdoor sector. With a broad product portfolio, the company meets the needs of mountaineers and cyclists, as well as other outdoor enthusiasts. The company now employs around 650 people at its headquarters.

12 Months
only were needed to integrate 121 suppliers on Retraced
95%
of suppliers actively participate & engage with Retraced’s capabilities
350+
certificates and audits managed centrally on Retraced
Embedding Sustainability into Every Decision at VAUDE
Environmental considerations have long played a major role at VAUDE, but it was only under the leadership of Antje von Dewitz that sustainability became a central component of the corporate strategy. At VAUDE, all corporate decisions are made with sustainability in mind, and an interdisciplinary team ensures that these principles are anchored in the day-to-day business of all areas of the company.
Bettina Roth, Head of Quality Management & CSR Supply Chain at VAUDE, has been working with various teams for years to implement the sustainability strategy within the supply chain. This commitment, coupled with developed expertise for transparent and responsible procurement has led VAUDE to actively involve its suppliers in sustainable transformations. In the meantime, a specialized team has been established to continuously develop the supply chain and align it with their sustainability goals.
"We introduced Retraced to comprehensively digitalize supply chain management at VAUDE. It is crucial that not only quality and delivery compliance can be monitored, but that social and environmental aspects are also considered."
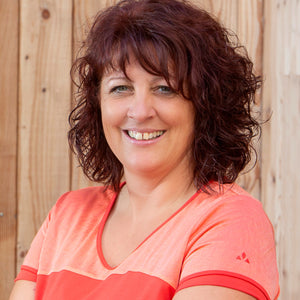
Searching for the Right Approach: The Decision for Retraced at VAUDE
After the VAUDE team evaluated various solutions for supplier management, it quickly became clear that there were different approaches and methods.
The decision was made in favor of Retraced, due to the platform’s bottom-up approach which aligns seamlessly with VAUDE's own. Given that the onboarding process for sewing companies or material suppliers often occurs one to two years before production, including checking the standards in the supplier's company, certificate collection, audits, site visits, sample production, and integration into internal processes, VAUDE sought a solution facilitating early-stage supplier integration, as well as comprehensive data collection and analysis, before materials or products enter the factory.
"In Retraced, we have found a solution to develop our supply chain sustainably and achieve the goals of our sustainability strategy. Retraced supports us in determining key figures, assessing the status quo of a supplier, presenting the supply chain transparently, managing certifications and audits, tracking the origin of materials (chain of custody and tracing) and ultimately providing this information to end customers in the medium to long term."
Implementation and Acceptance: The Roll-Out of Retraced at VAUDE
Once VAUDE decided to implement Retraced, a detailed roadmap was drawn up to successfully carry out the project. Roth explains: "The first step was to get the supply chain partners on board. Through phased integration, we onboarded our most important suppliers onto Retraced via kick-off meetings, training, and continuous dialogue, ensuring their active involvement and participation." Within just 12 months, VAUDE successfully integrated 121 suppliers on the Retraced platform and achieved an active supplier rate of 95 percent.
A key factor in the success of the project was Retraced’s user-friendliness for the suppliers. VAUDE placed great importance on ensuring that the system also offered benefits for the suppliers and was easy to use, as ensuring their willingness to participate was essential.
The implementation included training the suppliers so that they could enter their master data and certifications into the system. At the same time, the VAUDE team worked on how best to use the tool internally (for example: to check certificates and for validity reminders). With over 350 shared certificates on the Retraced platform, VAUDE has significantly optimized its processes.
The introduction of Retraced also impacts the relationship with VAUDE's suppliers. Roth explains that the suppliers recognize the advantages of such platform systems: "Retraced reduces extensive email chains and redundant manual work." However, she also emphasizes the importance of continuous exchange to improve the platform's use and benefits.
In an ideal scenario, the supplier enters their data into Retraced once, and then shares it with their customers, including VAUDE. This significantly reduces the workload. The aim during implementation was to highlight the benefits for the supply chain, and to move away from the flood of emails that go back and forth and need to be answered, to a system that makes workflows simpler. Instead of repeatedly dealing with manual data maintenance, Retraced allows data to be properly maintained and then linked to all customers, which means a significant reduction in manual work.
For VAUDE, the introduction of Retraced is an important step towards further improving transparency along the global supply chain and strengthening cooperation with suppliers. VAUDE is also in contact with other Retraced customers to share experiences on supply chain transparency.
Efficient Supply Chain Management and Resource Optimization with Retraced
VAUDE currently uses the Retraced platform to map the entire supply chain, including all master data. "We use Retraced's assessment to retrieve information from suppliers and track certifications. We want to use the platform's risk management capabilities down to the factory level to conduct comprehensive risk assessments. All of this enables us to improve transparency and control along the supply chain, identify potential risks at an early stage and derive targeted measures," explains Bettina Roth.
Retraced increases the efficiency of various teams at VAUDE in contact with supply chain partners. What previously had to be maintained in large Excel spreadsheets is now neatly organized in Retraced.
"Collecting data from the supply chain for our various reports such as the Sustainability Report, Textile Partnership Progress Report, etc. always caused us a lot of manual effort at the beginning of the year. By automating processes and centralizing data management, resources can be used more efficiently to focus on strategic tasks."
Future Steps and Collaboration with Retraced at VAUDE
"In the future, we also want to use CAPA management, integrate our internal audit management into Retraced and enable product traceability," says Bettina Roth, describing the next steps for VAUDE. Another focus is on data preparation for various stakeholders in the company. General management requires different information than, for example, supplier management or technical experts. The development of customized dashboards is intended to help meet the information needs of different interest groups and improve the effectiveness of management.
Overall, VAUDE will continue to work closely with Retraced to make the best use of the system, improve internal processes and meet the requirements of various stakeholders and legal requirements.
Header image: VAUDE / Markus Geber
Explore How Retraced Can Transform Your Supply Chain
Interested in achieving seamless supply chain transparency and staying ahead of compliance requirements? Discover how Retraced can empower your brand to manage supplier relationships, enhance traceability, and proactively handle sustainability challenges.